Yellow, is a very big challenge for elastic fabric in finishing, storage and transportation, especially for white or light color fabrics.
Yellowing may cause complaints and conflicts between fabric producers and customers. Moreover, it will cost much money and time to avoid or eliminate this problem.
So there is no reason to ignore this problem.
In general, textile producers must deal with the yellowing caused by temperature and storage. However, yellowing of elastic fabrics is a more complex phenomenon that should be avoided. To a certain extent, yellowing may be caused by heat setting, shaping, storage.
The yellowing tendency of elastic fabrics varies depending on the material and the fiber additives used.
On the contrary, the diversity of customers and high demand are:
High white color and high brightness
Low yellowing when finishing (color matches original sample)
Phenolic yellow evaluation mark 4 is the lowest standard, as storage yellow bottom line
The finished product has a final pH of 4-7
Prevent exposure to Nox
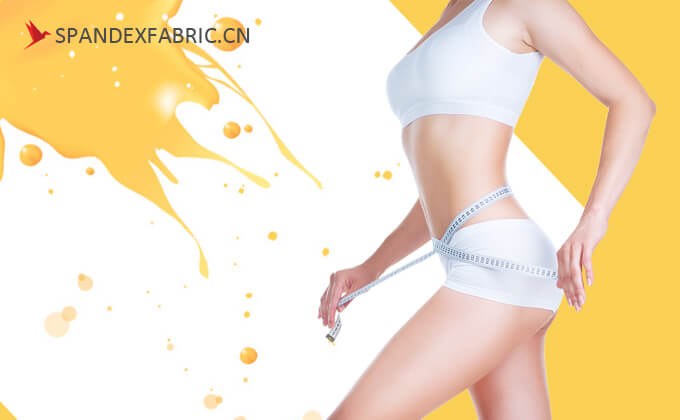
▲The reasons of elastic fabrics become yellowish
Heat yellowing
Firstly, the greige fabric is heat-set on a gas tenter, which will cause severe yellow due to touch heat-finishing (forming) and bonding, especially sensitive for elastic fabrics made of polyamides and polyesters. These problems will be worse when microfiber products exhibit the extremely large surface area.
There are more and more problems caused by cotton / spandex blended fabrics. Easily yellowing when heat-setting to eliminate curling to obtain sufficiently stable dimensions. The fabric will usually turn brown after finishing the process. Therefore, it must pass the time-consuming and costly scouring and bleaching process to achieve the desired whiteness.
In order to prevent the heat yellowing, special auxiliaries have been designed to prevent or minimize yellowing.
Yellowing caused by Nitrogen Oxides.
Exposed to the nitroxide gas, the yellowing of polyester or polyamide fabrics depends on the spandex content- more or less shows a slightly yellow to reddish color change.
The deposition of fiber lubricants and the fabric additives have an additional effect on fabric Nitrogen Oxides yellowing.
In practice, we always come across high Nitrogen Oxides concentrations, such as those generated during heat setting (e.g. gas stenters), warehouses (e.g. truck exhausts), and some atmospheric contaminants (e.g. smoke).
The effects of exposure to nitrogen oxides depend on the extent of damage. Constantly the damage is discovered in some weeks.
Common antioxidants normally used to prevent heat yellowing and phenolic yellowing are not enough to resist the effects of nitrogen oxides yellowing.